Category
Request from Us
Welcome to Walmat Engineering and Automation Systems Limited
New solar project
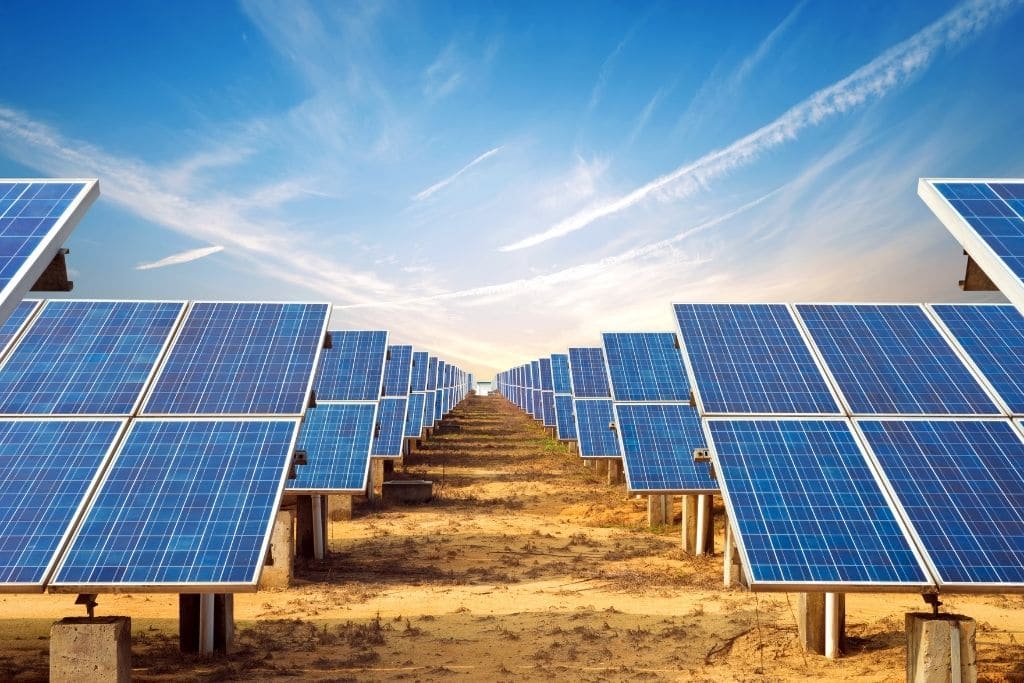
Msata solar project 650 mw
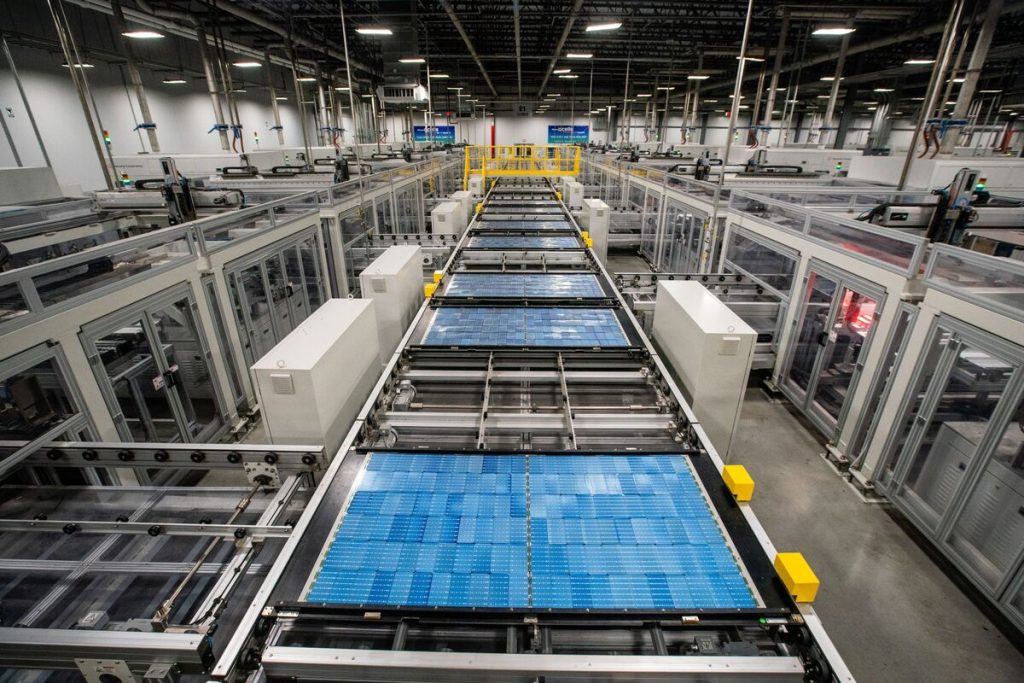
Solar Substation 32mw
MEP Design & Coordination System
THE MEP DESIGN OF BUILDING SERVICES
Overview
People in urban settings spend between 80 and 90% of their time in indoor spaces both during
work and during leisure time. It is therefore important that the Architect and the Mechanical,
Electrical and Plumbing (MEP) engineers work in unison to ensure the quality environment. A
good design can result in:
• Healthy and comfortable living
• Better environmental control
• Operational efficiency
• Lower greenhouse gas emissions
• Increased productivity
MEP ENGINEERS DEVELOPMENT PROGRAMS
Heating, ventilating, and air-conditioning (HVAC) systems account for nearly 40% of the energy
used in commercial buildings. The condition of your building envelope strongly influences HVAC
system energy consumption and occupant comfort. Outlined below are strategies that can be
used in buildings to conserve energy.
Building Orientation
Orientation of a building should be done for the climatic zone in which the building is situated.
• Cold climates: The South facing side provides maximum solar gain. Locate the building’s
axis on the East-West direction with its longest dimension facing the South.
• Hot and dry climate: During summer, the North wall gets significant exposure, and the
West side absorbs the maximum late afternoon heat. Similar to cold climates, longer walls
of building should face North and South with longer axis along the East-West direction.
• Warm and humid climate: In this climate, buildings should ideally be long and narrow to
allow cross-ventilation.
The optimum building orientation is somewhere along the east-west direction
MEP engineers must recommend a wall with low conductivity (U-value or high R-value) to resist
the heat gain or heat loss. High thermal mass (greater thickness) of material is preferred as this
means high thermal storage capacity and less heat flow.
Insulation
Insulation resists the heat flow through the building envelope. The energy consultants typically
recommend wall insulation resistance between R-11 and R-19 and roof between R-19 and R-30.
Glazing in façades
The glass in the building has a big influence in heat gain or heat loss. The following characteristics
of glass can be used to promote energy efficient design.
Day lighting and Ventilation
Arrange buildings to ensure good access to daylight and ventilation for nighttime cooling. Place
important spaces and windows at southeast corner of the site; it will get more sun in the winter
and less in the summer.
The depth of the building should not be more than 40 – 50 ft. Place windows on the south side to
get winter sun into the space. Use northern windows for even daylight throughout the day.
Shading devices
Shading devices should be used to avoid unwanted heat gains. Use architectural
overhangs/fins/louvers and to some extent deciduous vegetation to block solar rays in the
summer.
• Horizontal shading elements are appropriate on northern façades; and
• Vertical fins or moveable louvers are suitable on east and west façades to block solar
rays.
Color
The color of building affects heat absorption. The dark colors absorb more heat than lighter colors.
• In cold climates, the external surfaces of the walls should be dark in color for high
absorptivity to facilitate heat gains.
• In hot and dry climates, light shade colors (having low absorptivity) should be used to paint
the external surface particularly roofs and east and west façades. Darker shades should
be avoided.
• In moderate climates, pale colors are preferable; dark colors may be used only in recessed
places protected from the summer sun.
BUILDING COSTS
• Site Costs: Site costs normally cover the owner’s initial land acquisition and development
costs for the project.
• Construction Costs: Construction costs are the portion of hard costs normally associated
with the construction contract, including the cost of materials and the labor and equipment
costs necessary to put those materials in place. Added to this are overhead costs, which
include both job site management and the contractor’s standard cost of doing business
(office, staff, insurance, etc.).
• Material Costs: Material costs cover purchase of materials, including local and regional
taxes, and shipping and handling costs, which include transportation, warehousing, and
in some cases security. In very remote areas or in overseas locations, shipping, handling
and other overheads may exceed the cost of the material.
Installation Costs: Installation costs include the price of labor and equipment to put
materials in place. Labor costs consist of base wages, taxes, insurance, and benefits, as
well as premiums for overtime or for working in remote locations. Equipment costs include
the direct cost of the equipment (whether it is a purchase amortization or a rental) and the
cost of an equipment operator, which sometimes includes support staff.
• Overhead Costs: Overhead costs associated with construction are usually referred to as
general conditions. These costs include those for field supervisory staff, additional
professional services staff, engineering consultants, as well as temporary facilities and
utilities, small tools, and a variety of safety and security equipment. Also included in this
category are bonds, permits, and insurance costs allocated to the project. Contractors and
subcontractors also incur general conditions costs.
• Soft Costs: Soft costs include a variety of costs incurred by the owner to move the project
forward. Design fees, management fees, legal fees, taxes, insurance, owner’s
administration costs, and a variety of financing costs fall into this category